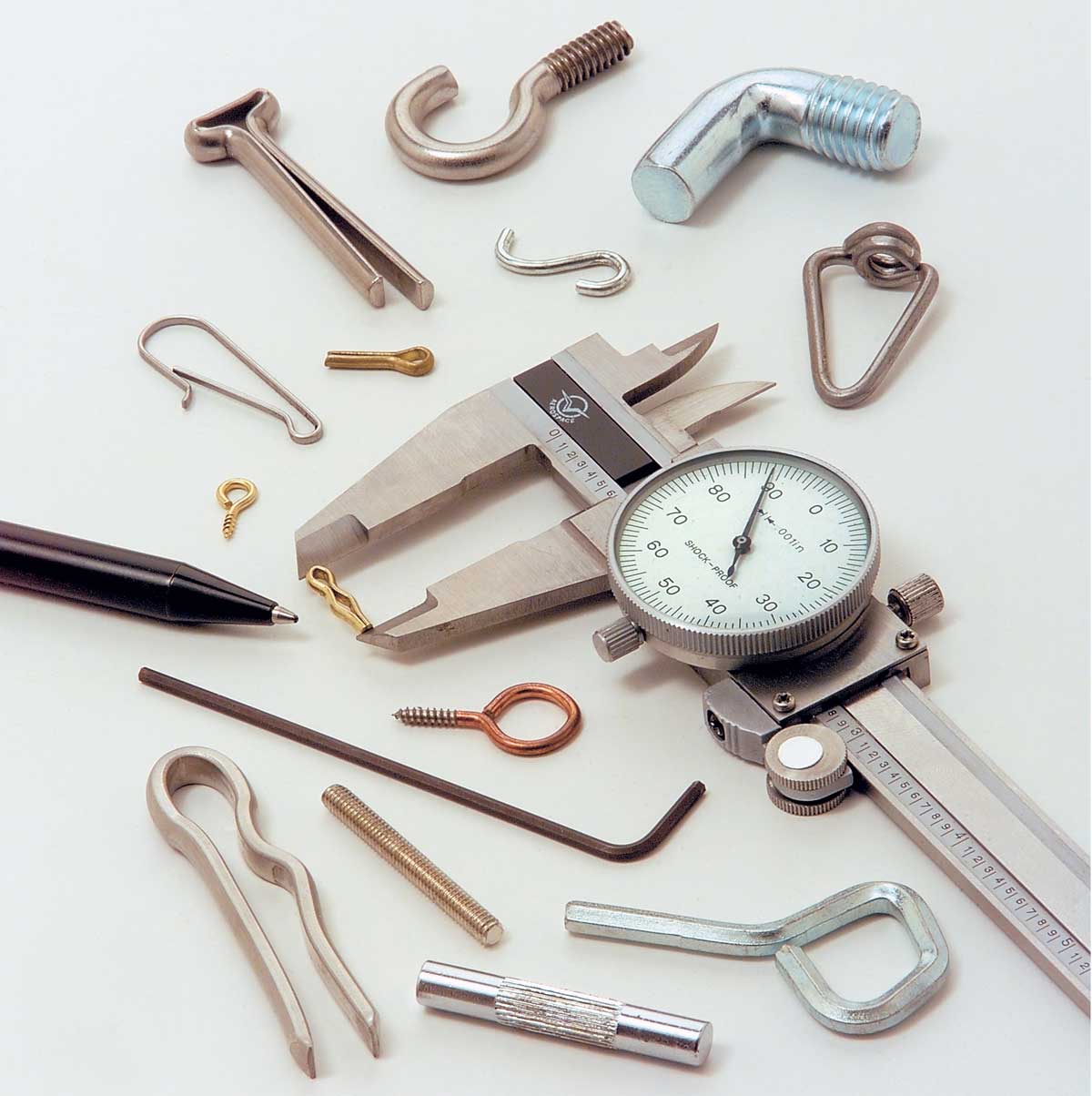
PRODUCTION EQUIPMENT
With our wide range of machinery, Hindley can fabricate parts which meet your specific needs. Our capabilities include forming wire in diameters from 1/32" to 5/8" and flat stock in various widths and gauges. Our fully automated machinery can economically produce both high and low volume orders.
- 75 4-slides ranging in wire diameter from 1/32" to 9/16" diameter and feed lengths up to 32".
- 6 forming and threading machines that can manufacture parts from 3/32" to 1/2" diameter, lengths up to 26".
- 2 OMCG Model 1200 with capability of 25 forming slides, up to 5/16" diameter wire with unlimited feed lengths.
- 1 OMCG CNC 16 three dimensional forming, requires no tooling
- 15 RMG Model 67 Autodraw In-Line Wire Drawing Machines
- 1 RMG Model 910 Autodraw In-Line Wire Drawing Machine
STANDARDS
Sort • Set in Order • Shine • Standardize • Sustain
Hindley is approved under the following standards:
- ISO 9001:2000
5S for a better work environment
Sort • Set in Order • Shine • Standardize • Sustain
These are the elements that make up "5S" that are used at Hindley. "5S" began as part of the Toyota Production System (TPS), the manufacturing method begun by leaders at the Toyota Motor Company in the early and mid-20th century. This system, often referred to as Lean manufacturing, aims to increase the value of products or services for customers. This is often accomplished by finding and eliminating waste (Muda)from production processes. "5S" has created the following results at HINDLEY that directly help our customers:
- Reduced costs.
- Higher quality.
- Increased productivity.
- Greater employee satisfaction.
- A safer work environment.